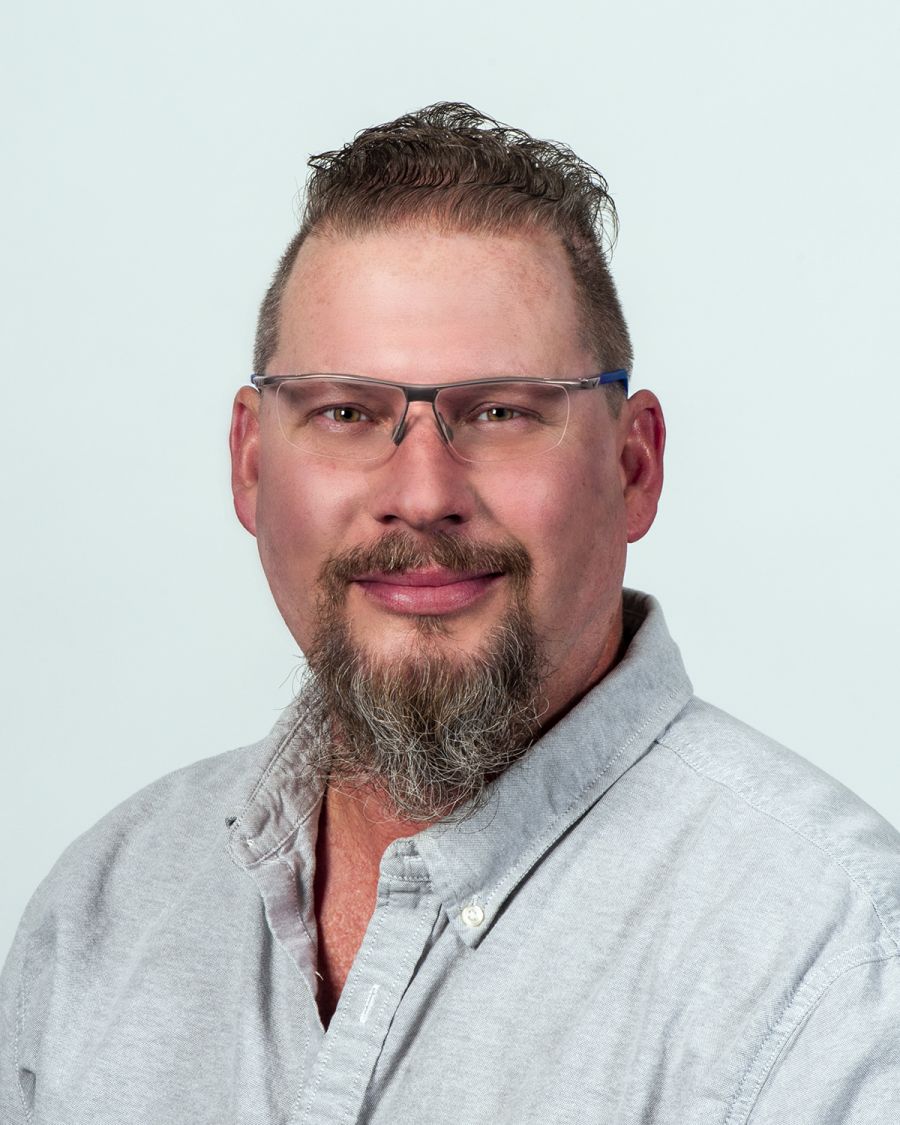
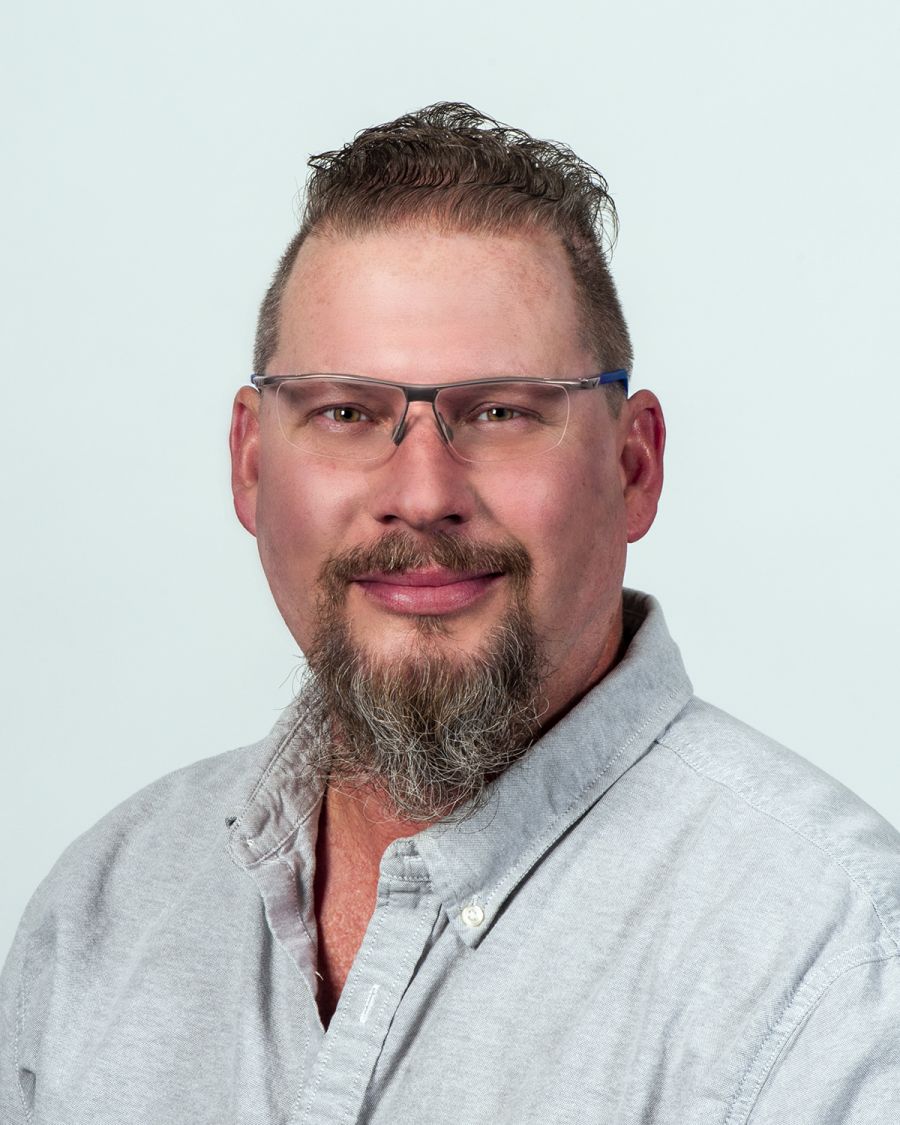
There I was, in a SCBA (self-contained breathing apparatus…) like you see firefighters wear and a full firefighting outfit to go back down into the reactor plant to check for a steam rupture. I was put in this wonderful outfit because I was the chief reactor watch, and supervised the mechanical watch-standers of that reactor plant. The reactor had been scrammed, the engineering spaces were hot (think sauna hot), and everyone had been evacuated. My “newbie” (newly qualified watch-stander) had reported to a steam rupture. While steam powers turbines, and powers your home through the electrical grid, it also quickly kills. So, there I was. I entered the engineering spaces through a hatch that was closed behind me… and down I went looking for evidence. By the time I got to the scene, my breathing mask was half full of my own sweat… my clothes were saturated… and I thought I was going to pass out from the heat. On an aircraft carrier, the engineering spaces are not air-conditioned. It is “ventilated” with nice hot air from whatever current area you are cruising. In an engineering space, with steam turbines, the temperature is typically 100 degrees F (unless you are lucky enough to be in the far northern or southern climates). We were not that lucky. But, I was young and enjoyed adventures. I eventually did find the evidence. A carbon dioxide fire extinguisher had ruptured (which had appeared to my watch-stander to be a steam rupture). I ran around to the various watch stations and placed the reactor plant in a safe and shut-down valve line-up. Imagine having to understand systems with hundreds of valves, their positions, and what purpose they serve. While filling my boots with my own sweat, I thought about how I got here. How did I go from growing up as an Air Force brat to a Navy nuke? Simple, the BIG PICTURE.
Today, I teach most of the classes in the Automation Technology Degree (AMT) Program at Waubonsee Community College. These classes cover areas such as electrical motor controls, programmable logic controls, hydraulics, pneumatics, mechanical power transmission, electronics, and mathematics. Some of the classes are completely online, some are completely in-person (lab heavy classes) and some are hybrid classes. A hybrid class allows the student to receive all lectures online, and spend time in class performing lab work. This allows greater flexibility for the student. A typical 16-week class meeting one night a week can now be completed in 8 weeks attending one night a week. Since all of the time in-person is spent performing lab work, the same amount of lab work is completed in 8 weeks.
Trained machine and process troubleshooters and technicians have their pick of jobs and careers both locally and nationally. Students typically end up as engineering technicians or automation technicians. There is never a job shortage; trained technicians are always in demand. The concepts taught in this field apply to many different sectors (manufacturing, power production, municipal, distribution and logistics, etc…).
This is not a program for everyone, but it is for those who want a logical structure, a path, and challenge to their future. Industrial controls are always evolving. There is always more to learn. If you want a constant challenge, want to update your skills, or just want to start getting into the area…this program is for you. This program of study is not memorization. It is based on understanding logical concepts. There will be study, reading, discussions, extensive lab work and reflection. All of this leads to the BIG PICTURE.
This elusive BIG PICTURE is gained through lifelong learning. Eventually, after much study, and much thought, your logical reasoning will change. This logical reasoning that you use to interact on a personal level with others will become the basis that you use to change your frame of reference and to interact with machine controls on a logical level. All areas become similar. All areas become one. Eventually, you will see that there is no difference between an on-off lighting system, a sequential manufacturing process, or a proportionally controlled hydraulic blow-molding machine. All of the systems follow the same logical concepts. When you become this person, you are invaluable.
The purpose of education is not simply memorization. The purpose of technical education is conceptualizing and understanding, and then applying those across a broad range of subjects.
Visit www.waubonsee.edu/manufacturing to learn more about the career opportunities and educational options in manufacturing.